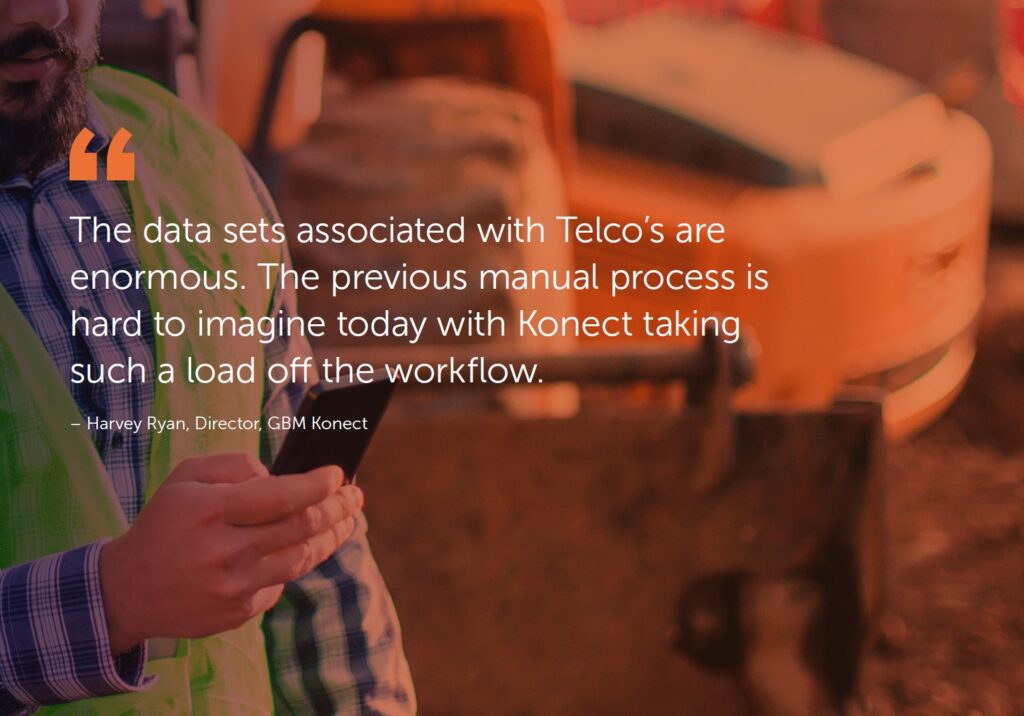
Picture the scene: Kilometres of telecommunication cable, hundreds of pits, dozens of premises and multiple work crews. There’s maps, notes and blueprints strewn across the bonnet of a vehicle and months of work ahead. Much of it will be writing notes, cross checking, fixing errors, reporting back and inputting data… manually! The evidence shows that 20% of the time can be wasted with workers driving up and down looking for the right work location – for some, that’s upward of $40M inefficiencies – and that’s just the start of the project!
GBM Konect Director, Harvey Ryan has been at the cutting edge of field management and mobile data collection for more than 40 years. He has led and delivered on significant project and product developments, and software innovation. The issues affecting Telcos, and in particular the roll out of NBN, is mirrored by dozens of other industries, and thousands of businesses. So how does Konect turn a Telco’s logistical predicament into a streamlined, productive process?
Harvey explains, “Prior to Konect, Optus were using GBM Mobile. When Konect hit the ground running, we were asked by Optus to provide 120 licences to help with their fibre roll-out. We were then approached by Downer, a leading provider of end-to-end technology and communications service solutions”.
Downer are one of the contractors responsible for ensuring the implementation of the Node to Premise (N2P) evolution and National Broadband Network (NBN) fixed wireless services.
So just how is Konect playing its part? Harvey continues, “The data sets associated with Telco’s are enormous. The previous manual process is hard to imagine today with Konect taking such a load off the workflow. Where once was pen and paper, PDFs, print photos and manual inputting, we now have a company like Downer using Konect to provide all the info required live, including task, status, problem, fix and reporting. Photos are uploaded to Konect immediately and then uploaded to Downer, which makes contract management so much easier. Captured images also help put together a whole work package including correspondence with the customer, plans, blueprints, aerial shots etc. all in the one place! Then, using Konect’s API, the data is synced between Konect and the Downer portal database”.
With Konect at the helm, the data is assured. Survey and construction phrases are being done sequentially and there’s no need for random work or searches, plus the elimination of double ups. “With map layers identifying the work, a simple click of the button shows the relevant worker the layer of map detail that they require. This may be Civils Work (cleaning, trenching etc.) or Hauling and Equipment. All work instructions are concise and with all of the relevant detail. All done spatially.”
Konect simplifies this most complex of workflows, and all the resulting benefits are hard to convey in few mere words. But, if revolutionising your workforce and boosting productivity with one app, one platform sounds like the best-in-class solution you are looking for, then now might be the time to get in touch.